About Campus Automotive
Nestled in the heart of Blacksburg, Virginia, Campus Automotive is where quality car care meets hometown service. Having taken over the shop in 2003, Matt McMurray has grown the business from its roots in towing into a full-service auto repair center. With 9 bays and more on the way, including a brand-new tire service, the shop’s not just bigger—it’s pulling in $300,000 more without needing to handle more vehicles, and that’s just 6 months after implementing Tekmetric.
Key to that success has been Matt’s right-hand man and General Manager, Johnnie Self. Johnnie has been running the shop’s operations and provides his unique background to ensure the team is always on top of the day-to-day. Combining his experience in the Army, 15-years as a police officer, and a degree in Organizational Management, Johnnie knows how to keep things in check. He learned from the ground up – including taking classes with the Automotive Repair Institute. A jack of all trades, Johnnie quickly understood the importance of a stable foundation, in this case, a shop management system that could keep up with Matt’s ambition and triple revenue without increasing fixed costs.
The Challenge
Campus Automotive initially relied on R.O. Writer, a point of sale system that, despite its initial appeal, fell short on updates and flexibility. This was particularly true in accounting and business overview capabilities. The limitations in accessing the system across different computers hampered Johnnie's high-level business visibility to track everything and make strategic decisions. To Johnnie, it didn't meet his standards of being user friendly.
Finding a solution
The journey to Tekmetric was a blend of frustration with the old way of doing things and the pursuit of a solution that offered more than just basic functionalities. Always looking for ways to improve, Johnnie was first introduced to Tekmetric at a Service Manager's coaching group in mid-2023. He had a conversation with his technicians and understood that the potential for seamless integration across the shop sounded like the right tool for the job. Johnnie's management style focuses on getting buy-in from his team. He wants them to have a say, and that's why after a technician recommended Tekmetric, he started investigating. It didn't take long before he looped in Shop Owner, Matt.
"Matt took one glance, called me that same night, and told me to make the switch. That was back in May of 2023. In our first 6 months, we’ve netted $300,000 more in revenue with the same amount of vehicles.”
Matt also had a friend who was using Tekmetric after transitioning from R.O. Writer and asked for a walkthrough. Since then, Tekmetric revolutionized the way Campus Automotive operated, with an all-in-one modern experience that Johnnie compared to the convenience of shopping at a superstore like Target or Walmart.
“Tekmetric changed the game for us. It’s like walking into a superstore but for car repairs—everything’s right there when you need it. Customizing work orders, ordering parts without the back-and-forth, and even adding videos to car inspections made everything smoother."
Features like custom RO labels, parts ordering, and Digital Vehicle Inspection Mapping with video additions to inspections significantly enhanced efficiency. The system's organizational capabilities and the option to have everything at one's fingertips stood out as game changers for Johnnie and his team.
Getting to a result
Implementing Tekmetric led to a transformative change in how Campus Automotive approached their business operations. The platform's automation and integrated systems not only facilitated a notable improvement in how appointments were set, but also completely improved transparency throughout the entire repair order process, particularly crucial in a college town where communication with customers—and importantly, their parents—is key. Matt’s goal of tripling revenue without increasing fixed costs became achievable, with the shop already seeing their average RO amount climb up 49% while maintaining their average vehicle count per a week.
“When your customers are college students and their parents are back at home, your shop needs transparency at every step.”
Transitioning to Tekmetric was smooth, with the entire team quickly adapting to the new system within a week. The elimination of paper-based processes and the clarity it brought to job assignments and technician accountability alone were huge for the team. Johnnie now has a “Command Center” setup with a large TV screen to display real-time shop activities that not only appealed to the younger technicians but also symbolized a modern, efficient workflow that Tekmetric enabled.
“We meet every morning around our command center 15 minutes before we open shop. It keeps us on the same page and lets us look through every single R.O. with advisors and technicians. If any of us are even 1 minute late, we dock a half-pay’s day. That includes myself. We go through it all and we address all the questions as a group to stay on the same page. It makes a difference.”
The takeaway
Campus Automotive’s experience with Tekmetric is a testament to its ease of use and the significant positive impact it has on shop operations. His advice to other shop managers and owners is clear: Tekmetric makes everything "EXTREMELY easy for everyone involved."
“The biggest change that we made last year that got us to this point is Tekmetric. It allowed us to be more organized on a daily basis – it’s up in front of me all the time, even right now!”
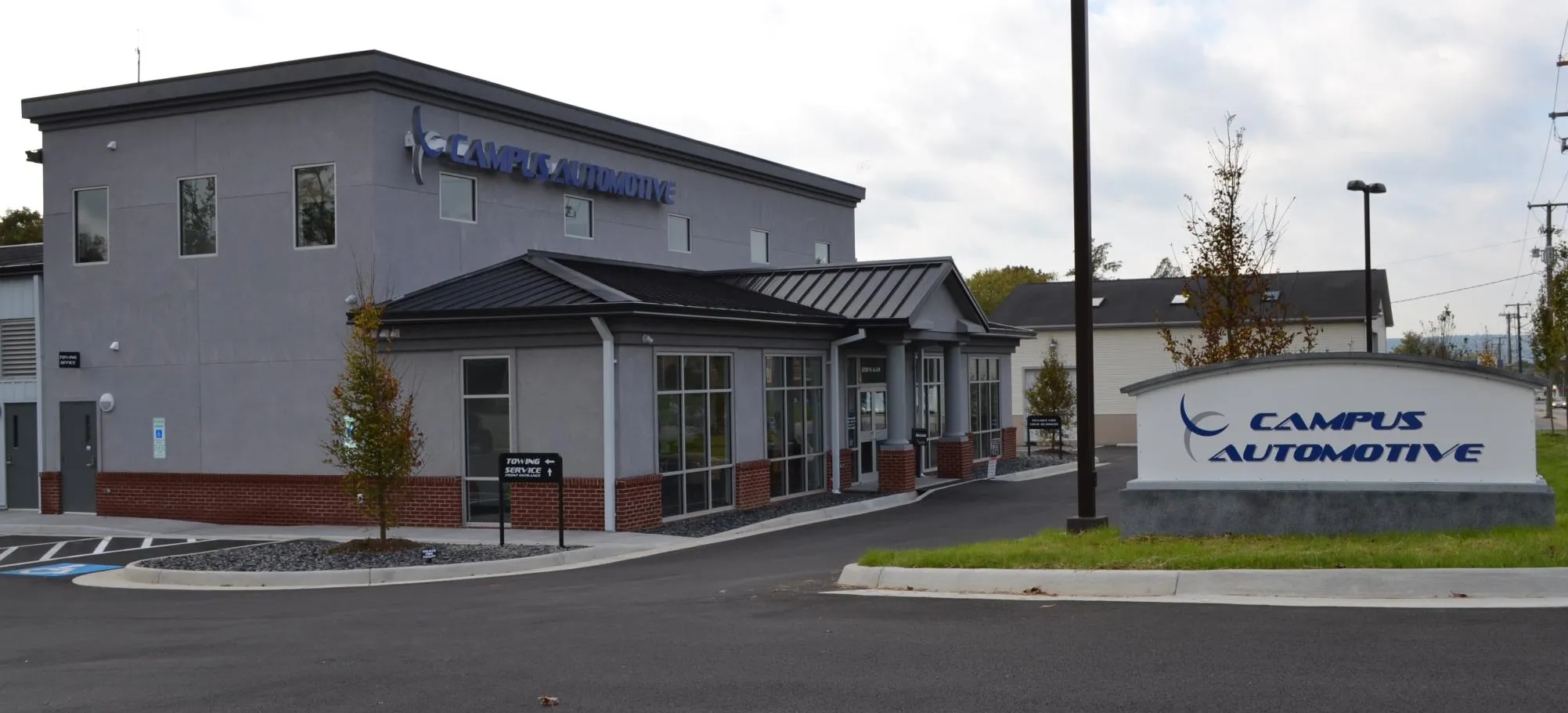